Being located in a picturesque corner of Cornwall poses no problems to Restormel Machine as the company grows its business, with customers from all over the UK recognising its ability to deliver on-time to high quality standards for turned and prismatic parts. Maintaining this reputation has been achieved through a programme of investment, with most of its extensive machine tool capacity being under three years old. The company’s purchase of an XYZ 710 vertical machining centre with five-axis capability is the latest example of meeting customer expectations.
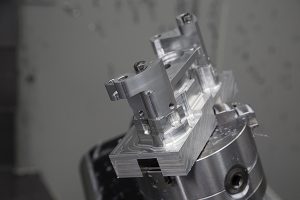
In addition to ongoing investment in machines and people, Restormel Machine’s managing director Barry Kennett highlights other factors that have seen the business grow significantly since it was founded as an owner/operator concern over 30 years ago: “We have had a natural progression over the years based on our ethos of providing efficient service and high quality. We also took a decision not to focus on any one industry sector, which has protected us to a degree from downturns, such as that seen recently in the oil and gas sector. Above all, we are happy to throw time and effort at jobs for customers to ensure that we build relationships and that they get what they want or expect. By providing this high level of support we overcome any perceived issues with our location. The overriding factor though, is that we must invest to move our business forward. If we don’t buy better, faster, more efficient machines we will just end up going backwards.”
As an already a committed customer of XYZ Machine Tools, with nine machines installed, when Restormel Machine was approached with some new work that would benefit from five-axis machining, it turned once again to XYZ. While the UMC-5X simultaneous five-axis machining centre is the flagship of XYZ’s VMC range, Kennett didn’t feel that he was ready to go to full five-axis; space was also a limiting factor. Therefore, he looked once again at the XYZ 710 VMC, of which he already had two, one of which with fourth-axis capability.
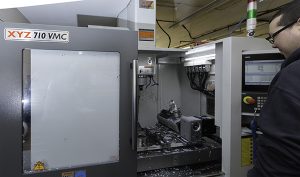
“Five-axis was definitely the next step for us, but with the pressure on space and our experience, going with the 710 VMC with a Lehmann five-axis unit fitted was the right move. This met our immediate requirements and has also opened other opportunities to bring in five-axis work. Additionally, while the move to five-axis was a learning curve, it has also encouraged us to review existing work that we produce using three- and four-axis machines. The result is that we are finding significant improvements in cycle times.”
These savings are highlighted by one component that was machined on a combination of three- and four-axis machines; the total cycle time across the two set-ups was 2.5 hours. By transferring this part to the XYZ 710 VMC, with the Lehmann fifth axis unit, cycle time was cut to just 50 minutes. In addition to improved machining times, having the additional axis also allows single set-up machining to be carried out, bringing additional productivity gains, with work in progress reduced as parts are not waiting around for the next operation.
“Having this capability has definitely helped us to not only secure existing contracts, but win new business,” says Kennett.
Another benefit of choosing the XYZ 710 VMC is the Siemens 840D ShopMill Control. Like many businesses, finding the right skilled people is a challenge, one that Restormel is addressing through apprenticeships. The Siemens control with its ‘JobShop Concept’ helps to overcome any skill/experience issues as it is truly conversational and provides easy to understand prompts in order to create simple and complex programs in the background.
The end result can then be viewed in plan, three planes or full 3D, to provide the reassurance that a user may need.
“The control is so easy to use and straightforward enough that our operators are able to switch from other machines using different brands of control,” says Kennett. “So confident in it are we that the machine is operated on a regular basis by one of our apprentices, who is using it to advance his skills set. “When he is not at college he is setting, programming (in five axes) and operating the machine without any issues whatsoever.”
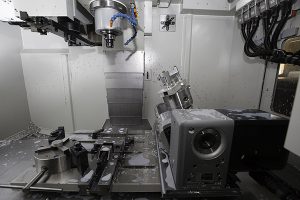
The XYZ 710 VMC installed at Restormel Machine features axis travels of 710 x 450 x 500 mm in X, Y and Z, with a table size of 760 x 430 mm, which the company makes full use of, with multiple set-ups on the table at any one time. Based on a solid cast iron structure, the machine features box slideways on all axes; the rigidity generated by this construction allows Restormel Machine to maximise available cutting-tool technology with increased cutting data. This is backed up by the 17 kW, 8000 rpm spindle, 20 m/min rapids and 24 station arm-type tool changer fitted as standard.
For further information www.xyzmachinetools.com