Established in 1967, Stevens & Carlotti produces metal fabrications at its Sandwich, Kent factory for customers in the UK and continental Europe. A jump in turnover of 25% in 2017 compared with the previous year looks set to be followed by a further 50% increase in 2018, which has unsurprisingly caused some production and logistical issues. The situation has resulted in an increase in headcount from 70 to 100 staff in the past 18 months, as well as a £1.5m investment in new machinery since September 2017.
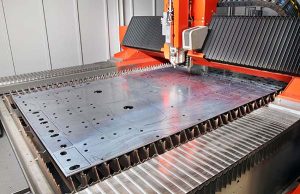
Part of this sum was allocated to the purchase of a Bystronic fibre laser-cutting machine of 3 x 1.5 m sheet capacity, together with two press brakes from the same manufacturer. The three machines are installed in one unit, forming a lean production cell on the Sandwich site for processing mild steel and aluminium from 1 to 25 mm thick, and stainless steel up to 15 mm.
Managing director Marco Carlotti says: “Orders have flooded in recently across the board for batch sizes ranging from one-off to several thousand. They are being placed by existing and new customers, from sectors such as power generation and pumps, through street furniture and road sweepers, to electronics, filtration and construction. Our success is partly because we offer a complete subcontract solution, including cutting, bending, machining, welding, assembly and painting.
“Several cutting methods are in use here, each of which has specific advantages that give our customers best value for money,” he adds. “Laser cutting is the lead technology, however, and we have been using CO2-powered equipment for nearly 20 years.
“Due to the current higher level of business, we decided to replace one of our two second-generation 4 kW CO2 machines with a Bystronic ByStar Fiber 3015 fitted with a 6 kW power source and a ByTrans Extended automated sheet loading and unloading system. The benefits have been astounding. On thinner sheets, say around 5 mm, the machine is four to five times faster, accuracy of cut is better and it is possible to produce finer detail than on a CO2 machine. Fibre laser cutting is also not so expensive to run, as it consumes less electricity, does not need any laser assist gases and maintenance costs are lower.”
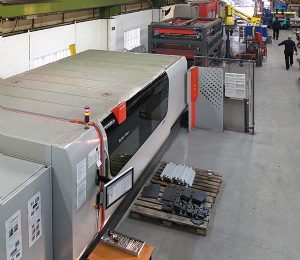
At the end of 2016, Carlotti visited the Euroblech exhibition in Hanover where it was obvious to him, and his two accompanying machine operators, that fibre technology had moved forward so quickly that it had become the new standard in modern laser cutting. Both of his incumbent CO2 laser-cutting machine suppliers offered a fibre alternative with automation, but he decided in favour of Bystronic following a visit to see the machines being built in the Swiss factory, which he describes as “impressive”.
The ByTrans handling system provides the best of both worlds in that it stores up to 6 tonnes of material, enough typically for a couple of hours’ lights-out production at the end of a day shift. Yet it also allows convenient manual intervention at a moment’s notice to fulfil a rush job if necessary. A tower system would not have been so flexible, due to the difficulty of accessing the shuttle table to place a sheet by hand.
Another feature of the ByStar Fiber that Carlotti likes is the control system, on which the interface is more akin to that of a tablet than a PC, making entering a program for an interim run easier. Conveniently, the same BySoft 7 software in the CNC system is also to be found in the controls of the latest Bystronic Xpert 150-tonne/3 m and 40-tonne/1 m capacity press brakes on site (the fabricator’s fourth and fifth from this source over the past 10 years). This software synergy speeds throughput when a component needs to be both laser-cut and folded.
An extra piece of Bystronic software that is about to be harnessed at the Sandwich facility is Plant Manager, which will provide visual support to the machine operator when planning which materials to stock near the machine for the next jobs, and when unloading cut parts. All components belonging to a particular customer order can be colour-coded on the cutting plan so that they are distinguishable from parts associated with other orders. Moreover, the first and last cut component can be labelled so that the operator knows when an order begins and when it is completed.
Carlotti concludes: “We have been impressed with the performance of the ByStar Fiber. The only problem we have is that it is so fast it can be difficult at times to feed the machine with the next sheet quickly enough.
“We are going through a major reorganisation of our site at present,” he continues. “As part of that, we will be rearranging the cantilever racking holding material for supply to the ByStar Fiber and will also be redesigning the breakout area to speed parts removal. If business remains buoyant and carries on increasing the way it has over the past couple of years, we will be looking to add an extension to the factory unit and integrate a tower storage system with the ByTrans to expand the cell’s automated production capability.
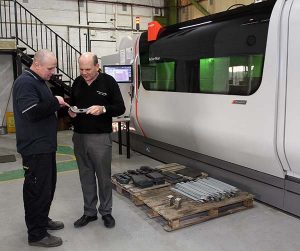
“Overall, the efficiency and accuracy of fibre laser cutting are allowing us to deliver competitively priced goods in a highly competitive industry, without having to compromise on quality or service. It is also helping to mitigate today’s higher material costs, so we do not have to eat into our margins too much.”
For further information www.bystronic.com